Kanban
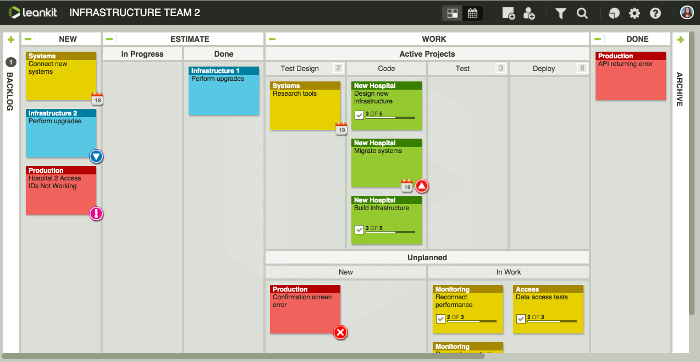
Kanban è una parola giapponese che significa etichetta, cartellino. Nell’ambito della logistica, indica un metodo di gestione degli stock, siano essi beni, materiali, compiti, prodotti in lavorazione, parti di software.
In senso più ampio è una gestione a vista di informazioni sui flussi di lavoro in sistemi produttivi just in time, fornendo informazioni puntuali per non sovraccaricare i lavoratori e intasare i flussi.
Il processo completo dell’analisi dei compiti dall’ordine alla consegna è consultabile da tutti i partecipanti, che svolgono i compiti secondo il loro turno di attesa.
Il kanban è un sistema che indica che cosa produrre, quando produrre e in che quantità. Limita i compiti da svolgere, per garantirne il flusso continuo e privo di intasamenti. Permette di equilibrare la domanda e la produzione. I flussi non sono spinti verso il cliente (push), ma sono tirati dal cliente verso di sé (pull).
Inventato da un ingegnere nel 1950, fin da allora fu applicato dalla Toyota nel suo metodo di gestione lean, che le permetteva di ridurre al minimo le giacenze di magazzino e di rispettare i termini di consegna grazie alla continuità del flusso di produzione.
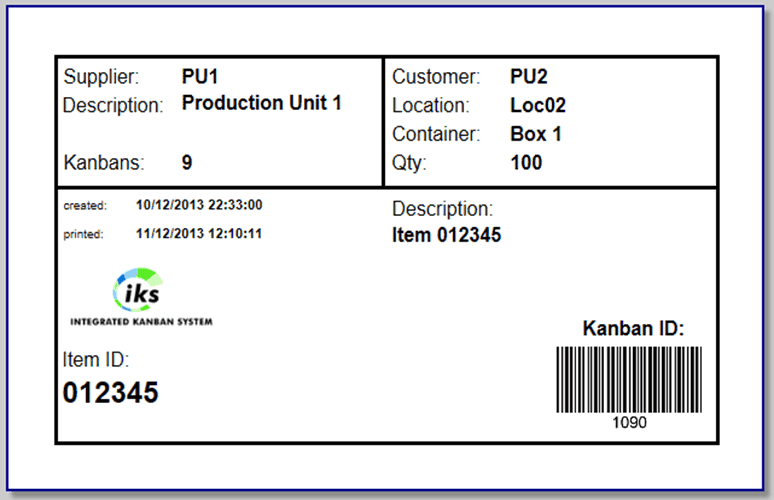
Consiste in una scheda di cartone con l’ordine del cliente e le caratteristiche e le quantità del pezzo da produrre, applicata su un contenitore vuoto che sarà riempito dal fornitore e inviato al cliente. L’immagine mostra una scheda-tipo per la produzione di 100 pezzi da mettere nel contenitore box1. Il codice a barre contiene gli stessi dati per lo scanner informatico.
Il flusso di lavoro è controllato a vista.
A che serve
- Ridurre i costi di produzione.
- Evitare la sovrapproduzione.
- Diminuire i ritardi.
- Migliorare la qualità.
I quattro fondamenti
- Comincia da ciò che fai abitualmente.
- Accetta l’idea di applicare miglioramenti continui.
- Rispetta i processi attuali, e i ruoli, le responsabilità e i titoli dei responsabili.
- Distribuisci la leadership a tutti i livelli gerarchici.
Le cinque buone pratiche
- Visualizzare i flussi per comprendere come funzionano i processi. Lo strumento più usato è un tabellone a colonne, che rappresentano i vari stadi di produzione e che può essere rappresentato anche su un monitor.
- Limitare il numero di lavori in corso per non creare ingorghi.
- Gestire i flussi seguendo il prodotto nei vari stadi di produzione.
- Spiegare bene i criteri per cui un prodotto in lavorazione passa da una colonna all’altra.
- Utilizzare modelli per riconoscere le opportunità di miglioramento.
Il metodo kanban è piuttosto semplice da applicare. Quando il cliente ordina un prodotto, per esempio 500 rubinetti per lavandini, si fa un cartellino che viene messo nella prima colonna del tabellone, o nel reparto che farà la prima lavorazione. Appena il reparto completa la prima fase, consegna i semilavorati con il cartellino al reparto successivo, oppure il cartellino passa nella seconda colonna del tabellone. Il processo si ripete man mano che la lavorazione va avanti, fino ad arrivare al magazzino e poi alla spedizione e alla fatturazione.
L’e-kanban è la versione web del metodo, che fa uno scan del codice a barre del lotto di produzione e lo segue lungo tutto il ciclo produttivo, anche se dislocato in luoghi diversi, generando un flusso di dati utili alla gestione generale dell’impresa, attraverso il costante controllo e l’ottimizzazione dei processi. I software di e-kanban possono visualizzare i flussi con timeline, mappe e schemi vari, o con un tabellone infografico in cui si muovono le schede virtuali dei singoli ordini in lavorazione.
E’ usato nello scrum e in altri sistemi agili di gestione dei progetti.